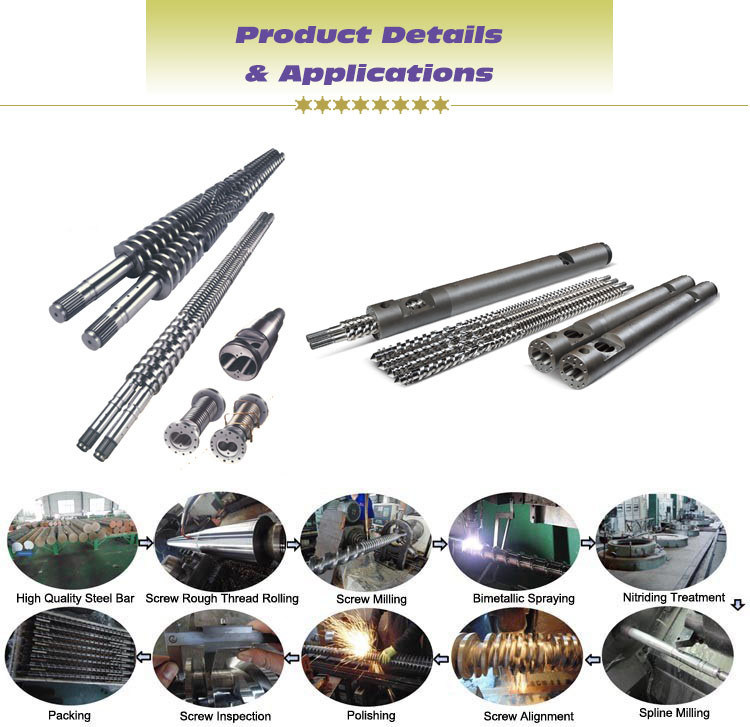
Technical Information for Conical Twin Screw Barrel | |||
Main Base materials | 1.38CrMoAlA (SACM645) | Main Alloy Materials | 1. Ni-based alloy/Deloro alloy |
2. SKD-61 (Special Tool Steel) | 2. Tungsten carbide/Wolfram carbide | ||
3. 42CrMo (Ultrahigh StrengthSteel) | 3. NiCo-based alloy | ||
4. DC53 (Cold WorkDie Steel) | 4. Fe-based alloy | ||
5. W6Mo5Cr4V2 (High-SpeedToolSteel) | 5. Co-based alloy | ||
Processing Technics | 1. Heat treatment | Technical parameters | Nitriding layer depth:0.5-0.8mm |
2. Quenching | Nitrided hardness:900-1000HV | ||
3. Nitriding treatment | Bimetallic layer depth:3 mm | ||
4. Bimetallic alloy welding for screw | Bimetallic hardness:57~69HRC | ||
5. Bimetallic alloy centrifugal casting for barrel | Hard-chrome plating hardness after nitriding:≥950HV | ||
6. Hard-chrome electroplating | Chrome-plating layer depth:0.03-0.09mm | ||
Linearity of screw:0.015mm | Surface roughness:Ra 0.4 |
The most common types of conical twin screw barrel extruder | |||
types of screw (d/D) | length of work(mm) | quantity ofextruder(kg/h) | speed of screw rotate(rpm) |
Φ35/77 | 810 | 40-70 | 5~50 |
Φ45/99 | 990 | 50-80 | 5~45 |
Φ51/105 | 1070 | 100-150 | 4~45 |
Φ51/105 | 1220 | 100-150 | 4~45 |
Φ55/110 | 1220 | 120-180 | 4~40 |
Φ60/125 | 1320 | 150-200 | 4~40 |
Φ65/120 | 1440 | 200-250 | 4~40 |
Φ65/132 | 1440 | 200-250 | 4~40 |
Φ70/140 | 1460 | 220-300 | 4~40 |
Φ75/150 | 1480 | 250-320 | 4~35 |
Φ80/143 | 1660 | 300-360 | 4~35 |
Φ80/156 | 1800 | 300-360 | 4~35 |
Φ90/184 | 2000 | 400-500 | 3~35 |
The most common types of parallel twin screw barrel extruder | ||||||
D35/5 | D45/2 | D50/2 | D60/2 | D65/2 | D70/2Â Â | D72/2 |
D75/2 | D80/2 | D85/2 | D90/2 | D93/2 | D100/2 | D105/2 |
D110/2 | D115/2 | D120/2 | D125/2 | D130/2 | D140/2 | D150/2 |
D160/2 | D170/2 | D180/2 | D190/2 | D200/2 | D200/2 | D250/2 |
Screw types:
Gradual change, chop, barrier, distributary, separate, air exhausting, pin, mixing and etc.
For good plasticizing effect, we have different design of screw barrel to meet customer's demand.
Specification :
Dia 20mm-250mm; L/D=15-45
Scope of Application:
1. Generally plastic material
2. Pipe/ Profile/ Sheet/Pelletizing
3. WPC, ABS, TPR, TPU, PMMA, C-PVC, UPVC, RPVC, PET, EVA, PU,PE etc
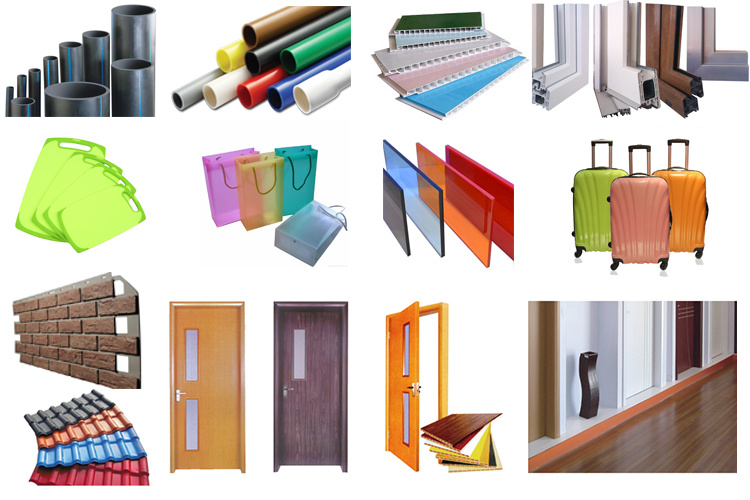
Treatment:
Nitrized, Chrome coating, Quenching, Bimetallic
We are foucs on each process to make sure each screw barrel is qualified according to technical requirement.Â
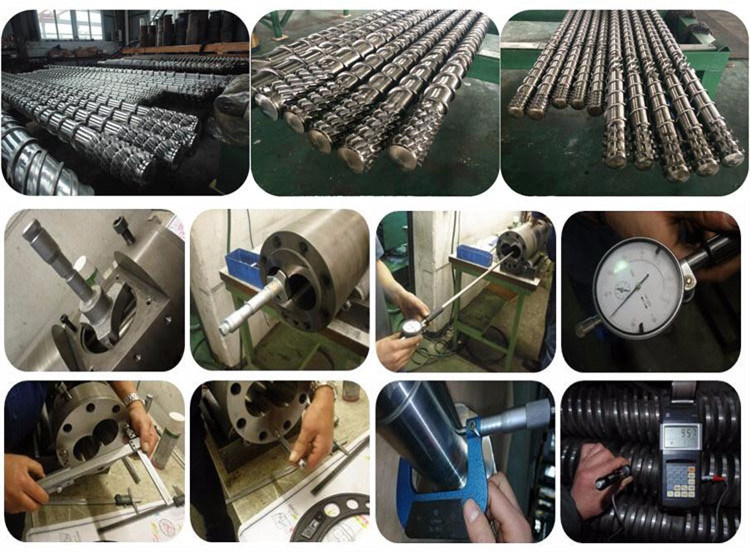
Packaging Details:
1. Be brushed anti-corrosive oil on extruder machine single screw.Â
2. Packed with film.Â
3. Packed in the AA wooden.
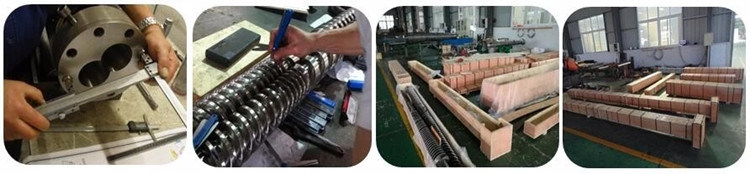
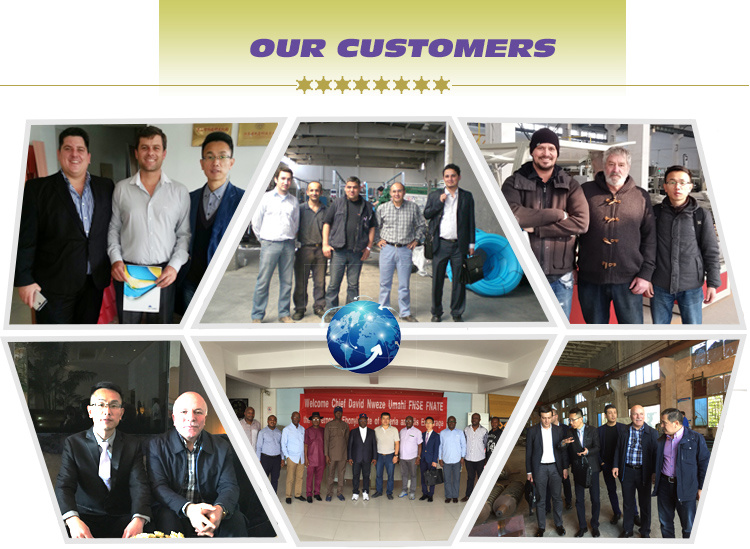
Please provide samples or requirements about dimensions and tolerances of , semi-finished and finished products, the equipment, the monthlly comsumption quantity, the current screw and barrel you are using, HRC and so on.
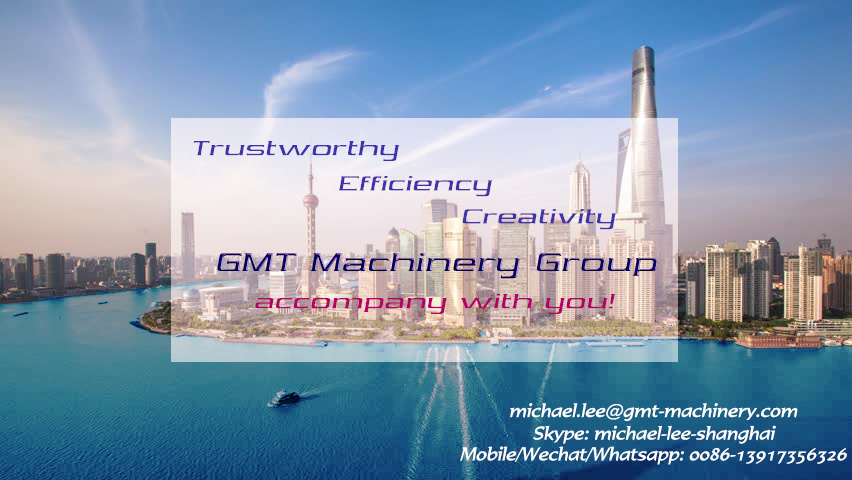
For more information, please kindly contact as below:
Mobile: 0086-13917356326
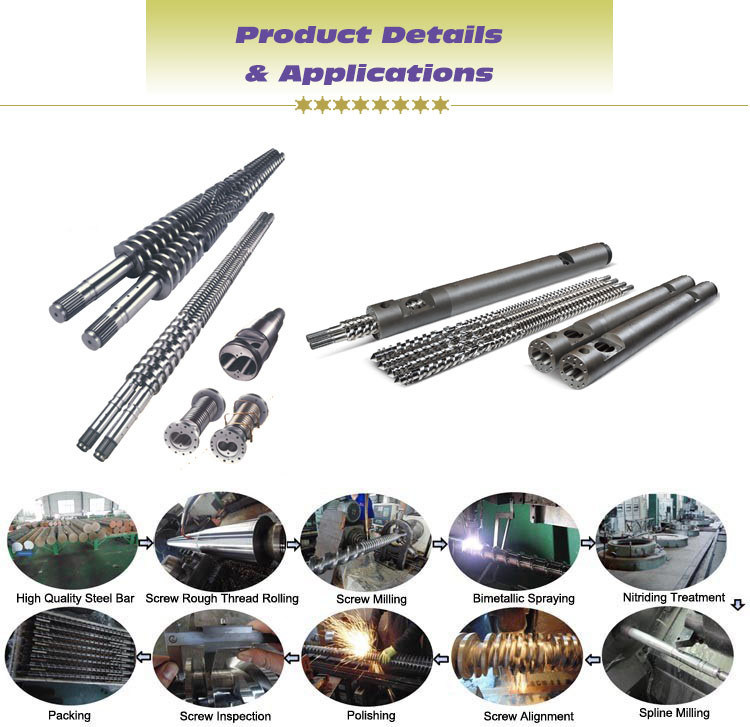
Technical Information for Conical Twin Screw Barrel | |||
Main Base materials | 1.38CrMoAlA (SACM645) | Main Alloy Materials | 1. Ni-based alloy/Deloro alloy |
2. SKD-61 (Special Tool Steel) | 2. Tungsten carbide/Wolfram carbide | ||
3. 42CrMo (Ultrahigh StrengthSteel) | 3. NiCo-based alloy | ||
4. DC53 (Cold WorkDie Steel) | 4. Fe-based alloy | ||
5. W6Mo5Cr4V2 (High-SpeedToolSteel) | 5. Co-based alloy | ||
Processing Technics | 1. Heat treatment | Technical parameters | Nitriding layer depth:0.5-0.8mm |
2. Quenching | Nitrided hardness:900-1000HV | ||
3. Nitriding treatment | Bimetallic layer depth:3 mm | ||
4. Bimetallic alloy welding for screw | Bimetallic hardness:57~69HRC | ||
5. Bimetallic alloy centrifugal casting for barrel | Hard-chrome plating hardness after nitriding:≥950HV | ||
6. Hard-chrome electroplating | Chrome-plating layer depth:0.03-0.09mm | ||
Linearity of screw:0.015mm | Surface roughness:Ra 0.4 |
The most common types of conical twin screw barrel extruder | |||
types of screw (d/D) | length of work(mm) | quantity ofextruder(kg/h) | speed of screw rotate(rpm) |
Φ35/77 | 810 | 40-70 | 5~50 |
Φ45/99 | 990 | 50-80 | 5~45 |
Φ51/105 | 1070 | 100-150 | 4~45 |
Φ51/105 | 1220 | 100-150 | 4~45 |
Φ55/110 | 1220 | 120-180 | 4~40 |
Φ60/125 | 1320 | 150-200 | 4~40 |
Φ65/120 | 1440 | 200-250 | 4~40 |
Φ65/132 | 1440 | 200-250 | 4~40 |
Φ70/140 | 1460 | 220-300 | 4~40 |
Φ75/150 | 1480 | 250-320 | 4~35 |
Φ80/143 | 1660 | 300-360 | 4~35 |
Φ80/156 | 1800 | 300-360 | 4~35 |
Φ90/184 | 2000 | 400-500 | 3~35 |
The most common types of parallel twin screw barrel extruder | ||||||
D35/5 | D45/2 | D50/2 | D60/2 | D65/2 | D70/2Â Â | D72/2 |
D75/2 | D80/2 | D85/2 | D90/2 | D93/2 | D100/2 | D105/2 |
D110/2 | D115/2 | D120/2 | D125/2 | D130/2 | D140/2 | D150/2 |
D160/2 | D170/2 | D180/2 | D190/2 | D200/2 | D200/2 | D250/2 |
Screw types:
Gradual change, chop, barrier, distributary, separate, air exhausting, pin, mixing and etc.
For good plasticizing effect, we have different design of screw barrel to meet customer's demand.
Specification :
Dia 20mm-250mm; L/D=15-45
Scope of Application:
1. Generally plastic material
2. Pipe/ Profile/ Sheet/Pelletizing
3. WPC, ABS, TPR, TPU, PMMA, C-PVC, UPVC, RPVC, PET, EVA, PU,PE etc
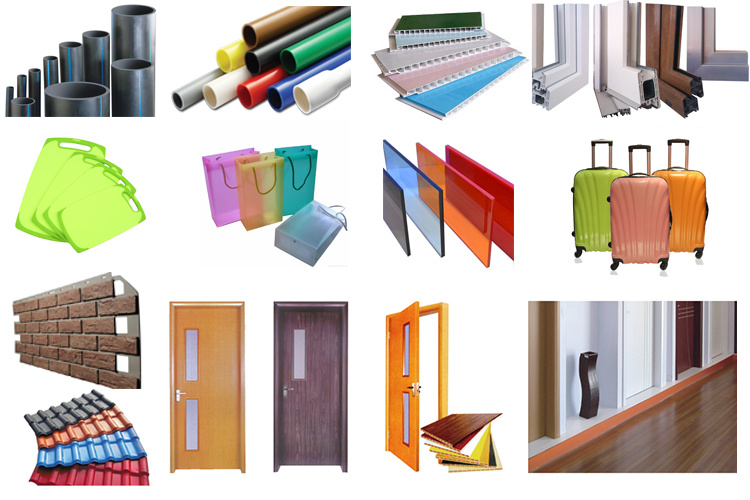
Treatment:
Nitrized, Chrome coating, Quenching, Bimetallic
We are foucs on each process to make sure each screw barrel is qualified according to technical requirement.Â
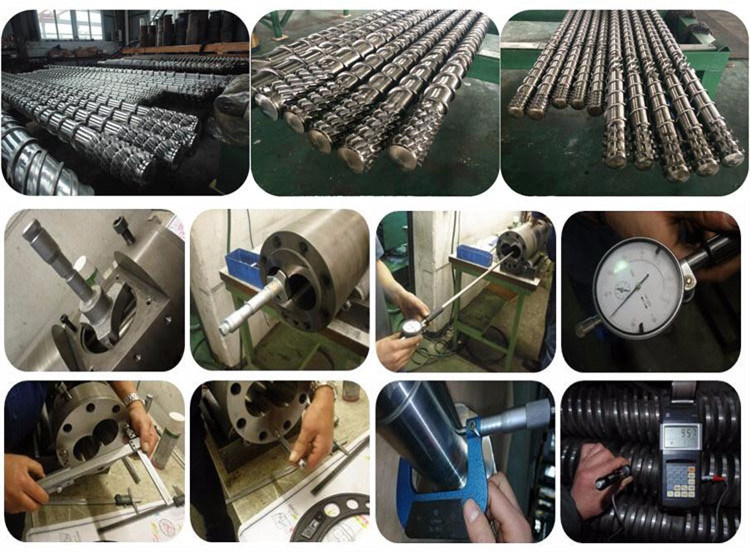
Packaging Details:
1. Be brushed anti-corrosive oil on extruder machine single screw.Â
2. Packed with film.Â
3. Packed in the AA wooden.
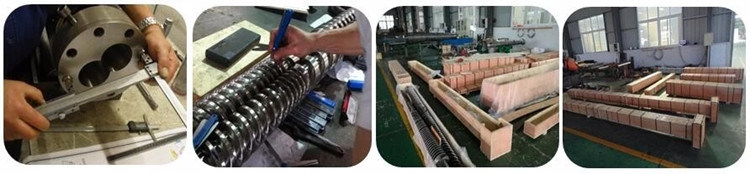
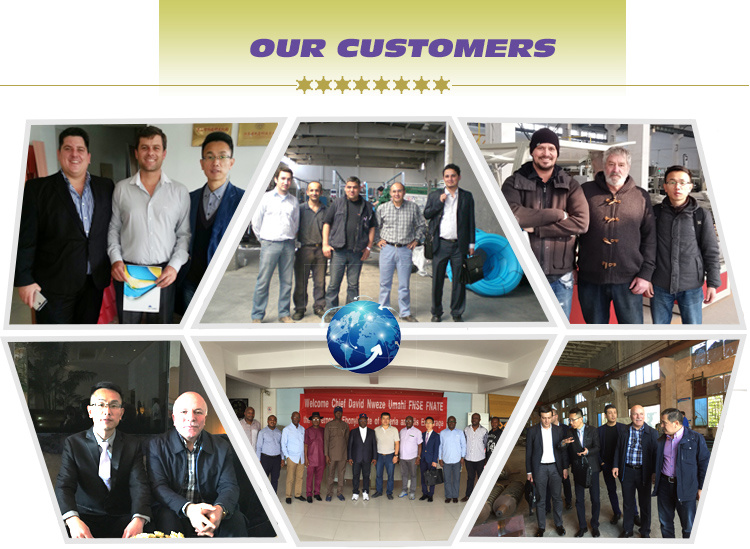
Please provide samples or requirements about dimensions and tolerances of , semi-finished and finished products, the equipment, the monthlly comsumption quantity, the current screw and barrel you are using, HRC and so on.
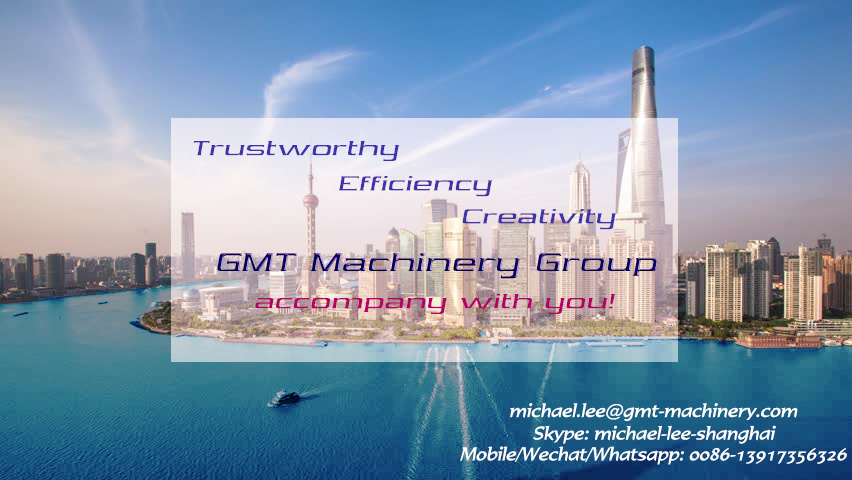
For more information, please kindly contact as below:
Mobile: 0086-13917356326
Truss Type Automatic Production Line
Truss Type Automatic Production Line
The integration of the truss
mechanical arm and lathe bed enhances the compactness and aesthetic
appeal of the machine tool, enabling more stable and efficient automated
production. Each standard machine
tool is equipped with interfaces for truss automation, including
columns, protective features, and electrical components, which
facilitate easy installation of automation systems at a later stage. By
mounting the truss column onto the lathe bed, a stable integration is
achieved, unaffected by variations in the foundation or any
displacements. The planning and
design of the system incorporate a low truss height, a low center of
gravity, and ensure smooth and stable operation.
Truss Type Automatic Production Line,Automated Truss Production Line,Fully Automated Truss Production Line,Automation Truss Structure Production Line
Ningbo Yien Machinery Co., Ltd , https://www.yiencnc.com